Кайдзен – в каждый цех
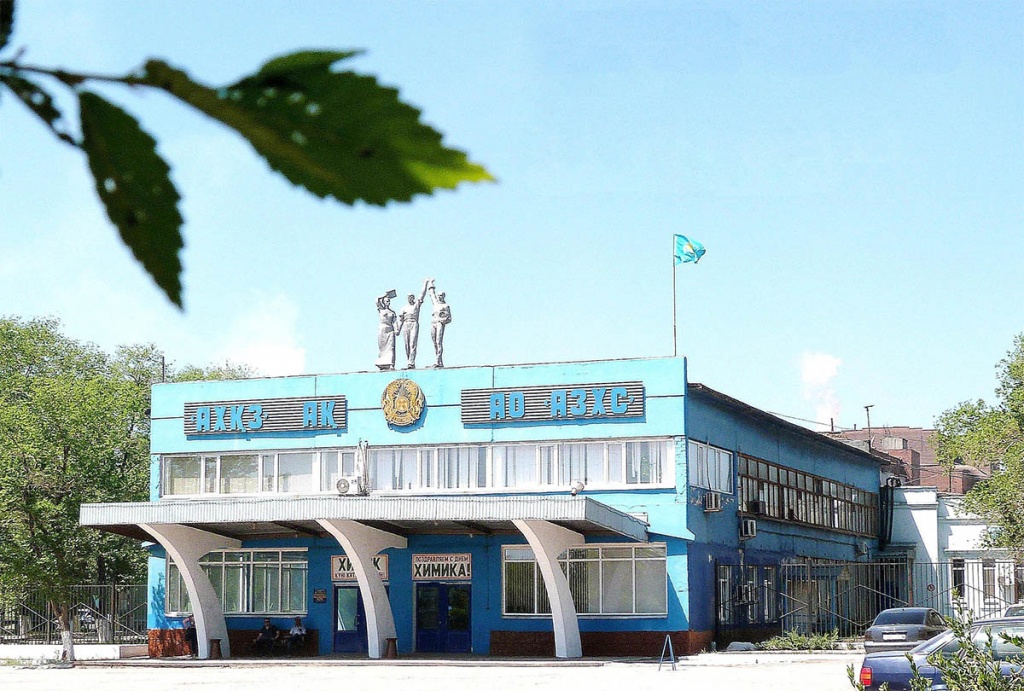
Японское слово кайдзен состоит из двух частей: кай – изменение и дзен – к лучшему (хороший). Если говорить проще, то это система, в основе которой лежит непрерывное улучшение всех процессов производства. Бывший работник завода, а сегодня кайдзен-тренер и консультант Виталий ЧИЧАЕВ помогает пересмотреть рабочие процессы и таким образом повысить эффективность производства Актюбинского завода хромовых соединений.
– Кайдзеном я начал заниматься ещё на заводе, когда работал в исследовательской лаборатории, – говорит Виталий Чичаев. – Тогда я ещё не знал, что это так называется, но понимал, что какие-то факторы мешают работать в полную силу. У меня не было инструментов борьбы с этой неорганизованностью. Потом я познакомился с кайдзеном и понял, что это и есть те недостающие элементы в моём рабочем процессе. Я заинтересовался японской философией и в 2019 году прошёл обучение в Кайдзен-центре в Алматы, где получил диплом кайдзен-тренера. Как известно, впервые кайдзен внедрили в компании Toyota после второй мировой войны. И это помогло им восстановить производство. Я пытался применить новую систему в рамках внедрения стандартов ИСО и увидел, что это реально даёт эффект. Работу, на которую раньше уходило два часа, теперь можно было сделать за полчаса.
На самом деле технологию кайдзен мы все применяем в обычной жизни: складываем аккуратно вещи на полках, в каждом доме есть место, где хранятся документы, проводим генеральную уборку. А вот на работе мы часто не обращаем внимания на то, как организован наш рабочий процесс и делаем всё автоматически.
– Задача кайдзен – заставить каждого задуматься о том, что и как он делает, – объясняет кайдзен-тренер. – Считается нормальным, если человек 15-30 минут ищет какой-то инструмент или документ, но никто не задумывается, что он теряет рабочее время, главную нашу ценность. Особенно это недопустимо на производстве.
Кайдзен – японская философия, которая предполагает постоянный поиск и устранение скрытых потерь. И устранять эти потери каждый день должны и работники, и руководители.
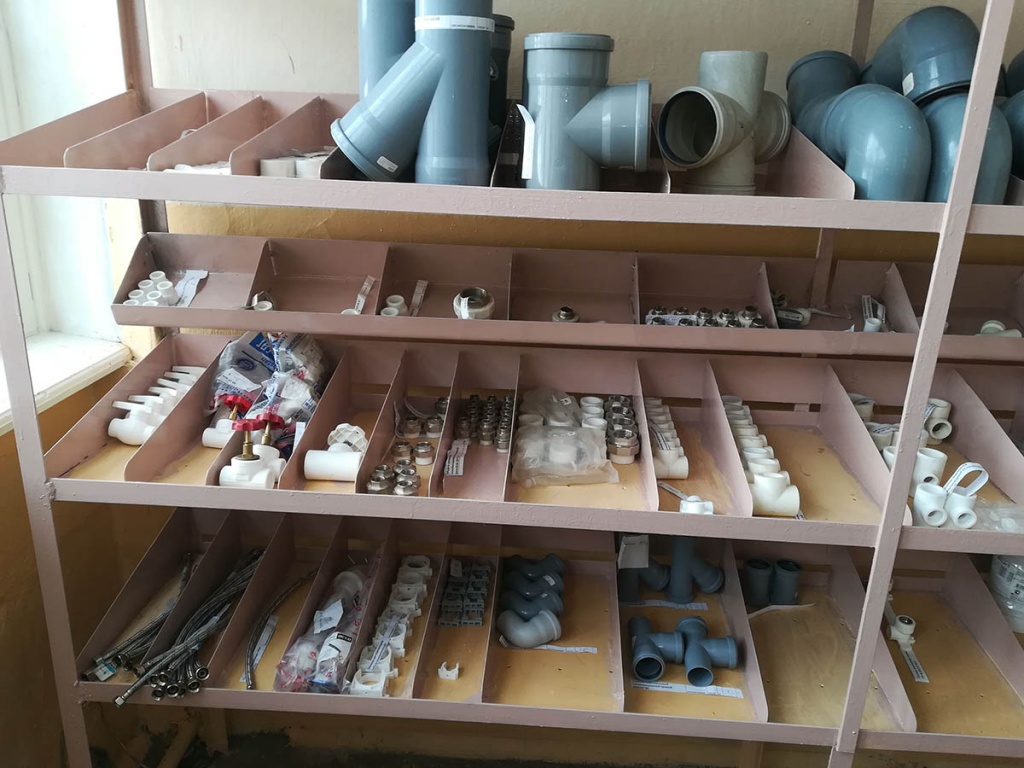
Всё на своих местах!
Проект бережливого производства на «АЗХС» начался пробно в цехе электроснабжения и электроремонта в марте 2019 года. К концу года уже были заметны результаты. Например, были организованы площадки для удобной и безопасной работы при замене электродвигателей. В 2020 году системой кайдзен охватили ещё 3 подразделения на предприятии – это ремонтно-строительный цех, энергоцех и складское хозяйство.
– Склад электротоваров – это большое количество наименований, обычно во время приёма-передачи склада одного завскладом другому долго разбирались, где что лежит, – разъясняет кайдзен-тренер Виталий Чичаев. – Мы пришли к тому, что выделили зоны на каждую продукцию, то есть не просто завезли и положили на любое свободное место, а всё по зонам раскладывают сразу. Белая зона – для неоприходованной продукции, красная зона – выключатели, жёлтая – лампочки и т.д. Теперь приём-передача электротоваров происходит быстрее. Работнику не надо бродить по складу: посмотрел цвет и нашёл нужный товар. Ещё один момент: весы стояли в углу, а материалы, которые взвешиваются, лежали в другом углу. Мы сделали перестановку: то, что взвешивается, поставили ближе к весам. Выделили место для получателей товара, они теперь не ходят по складу, а получают в одном месте. Такие, на первый взгляд, маленькие моменты позволили сократить всю ненужную суету и беготню. Внедрили карту ежедневного осмотра автопогрузчика, что позволило практически исключить аварийные остановки. Все неполадки выявляются на ранней стадии и своевременно устраняются.
В ремонтно-строительном цехе изготовили шаблон для производства башмаков для поддонов. Раньше каждый работник производил один такой «башмак», теперь один человек одновременно делает три «башмака». В результате освободилось одна единица оборудования для выполнения другой работы.
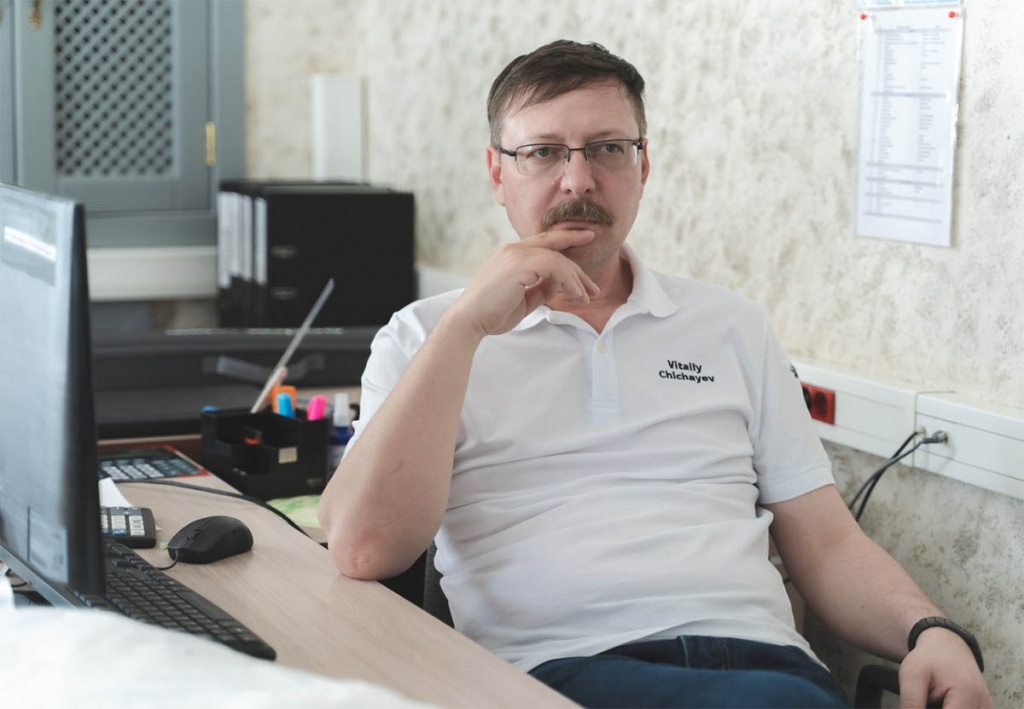
Работники вдохновились
И уже в прошлом году к системе «Кайдзен» привлекли основной цех по производству монохромата натрия АО «АЗХС», в котором улучшение работы каждого сотрудника начали с наведения порядка на каждом рабочем месте. Существующую систему целевых проверок по охране труда объединили с системой аудитов 5С (организация рабочих мест) для более качественной проверки оборудования и инструментов.
– Если раньше болты и гайки на рабочих местах хранились в одной ёмкости, то сейчас они распределены по типам и размерам для быстрого поиска. Сами работники почувствовали удобство и теперь следят за порядком – замечает кайдзен-тренер и консультант Виталий Чичаев. – Где-то работникам во время проверки весов больше не нужно поднимать наверх гири. Обновлены графики уборки рабочих мест. Они и раньше были, но сейчас чётко прописано, как сотрудник должен наводить и поддерживать порядок на своём рабочем месте.
Важно опыт Японии переложить на наш опыт. Провели обучение и руководящего состава и (обязательно) – для каждого работника. Самое главное, чтобы люди понимали, для чего это нужно. Сейчас работники завода говорят, что не хотят возвращаться к прежнему рабочему процессу. Они посмотрели на него под другим углом, перестроили – работать стало легче, и эффективность труда, можно сказать, повысилась. Заводчане уже сами хотят развивать и поддерживать эту культуру на предприятии.
В планах Актюбинского завода хромовых соединений теперь оптимизировать работу снабжения и внедрять бережливое производство во всех цехах. А когда есть вдохновение, то и работа ладится!